Processing, Grading & Packaging
Our focus is to provide farmers with high standard, graded and packaged seed
Seed processing is one of the most important activity to enhance quality of seed to next level. The seed is harvested from geographically dispersed production locations and is transported to VNR supply chain warehouse. These heterogeneous seed lots of varying quantities, arriving in processing plant are carefully handled by technically skilled, highly experienced and dedicated team. This team is responsible to take care of seed through various stages – arrival, weighment, storage, drying, fumigation, conditioning, treatment, packaging and dispatch. VNR Processing Plant follows standard operating procedures, protocols & quality assurance processes at every stage of seed handling.
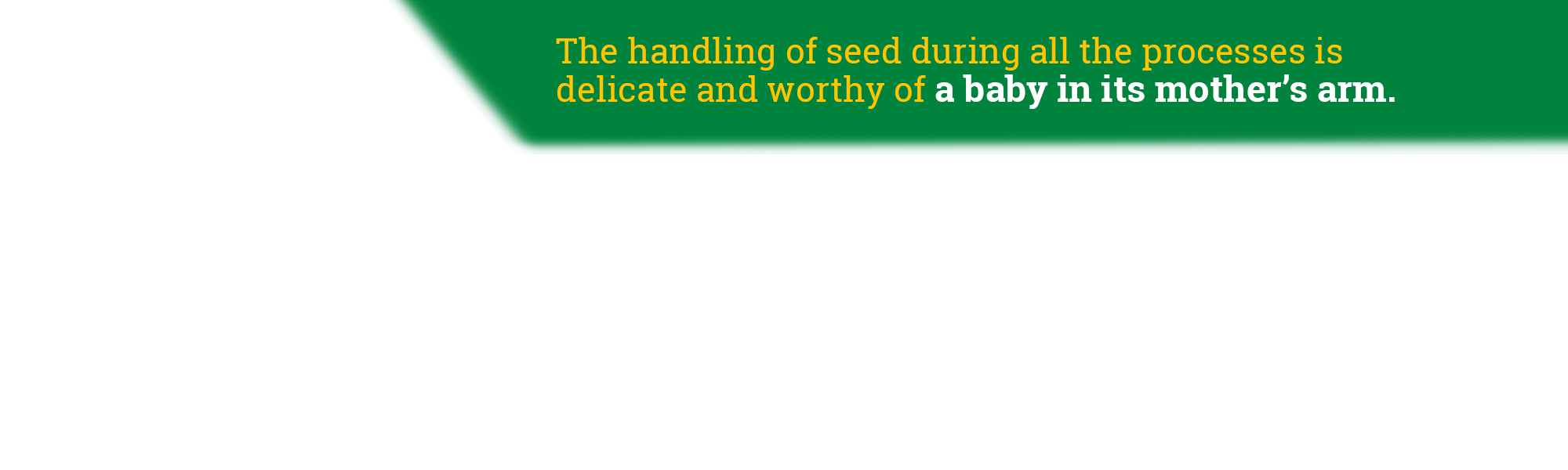
Objectives of Seed Processing
Processing Plants
The primary objective of processing is to deliver its end customer – Farmer – homogeneous and robust seed which are hygienic, sanitized and available in convenient pack sizes at the right time
Post arrival of seed from production field is subject to weighment through calibrated electronic scale. Raw seed is accounted for as inventory and stored in separate distinctly identified bins on palates.
The lots are constantly monitored for optimum moisture content, in case of moisture above than normal than seed is dried. Seed lots are fumigated for prevention of infections and infestations.
On arrival sampling of every lot is undertaken for initiation of various quality tests. For future reference guard sample is archived. Seed quality which is attained in production field needs to be emphatically preserved in processing plant while conditioning, packing and storage.
Seed lots when arrives from production fields carries different types of physical impurities like seed of other crops, ODV seed, weed seed and other foreign inert matters like straw, broken seed, stones, soil particles etc. Due to reason beyond control, seed may carry impurities including infections. Contaminated seed if sown will give lower yield. The physical appearance due to inconsistency of size, shape, color are sorted mechanically and with electronic aids to render homogeneity. Ideal season and pack sizes are determined and when the seed lots are declared quality fit they are packed, stored and later, dispatched to the dealer distributor network.
Availability of seed at the right time in market is dependent on timely dispatch by processing plant. This team in coordination with logistics department ensures that rightful pack sizes and correct quantities are dispatched against verified orders to distributor/dealer network well with in time.
VNR has robust system for product traceability. Distinct lot wise identity of seed in maintained. Lot and its subsequent batches based handling facilitates both backward – where it was produced and forward traceability – where it was dispatched. This helps in root cause analysis related to quality issues, if any reported from the fields.
VNR adheres total compliance to law of the land. All the processes implemented are as per the provision and rules prescribed in – The Seed Act 1966, The Seeds (Control) Order 1983 and other applicable regulations.
VNR believes in environmental sustainability. All infrastructure facilities are designed to support conservation of energy, water and natural resources. Minimize waste generation through reduction, reuse and recycle. Minimize pollutant, effluent, noise and odor pollution. VNR gives highest importance to the cause of Environment protection, Health and Safety. It follows standard protocols to handle incidents relating to health and safety so as to eliminate any form of injuries. The commitment to environment protection is clearly laid out in operational activities and every employee in every location take personal responsibility for reducing adverse impact on environment.
Pre-cleaning: This process is used to remove chaff, straw and dust before further processing of seed lot for fine cleaning. Pre cleaning machinery at VNR are versatile and can adopt to various processing requirements of shape and size. Their design incorporates multiple screen adaptability and multi-function adaptability for each screen leading to operational efficiency.
Fine-cleaning: Facilitates precise grading of under size and over size material, removal of light, immature and other impurities. Apart from multiple screen and multiple function i.e. interchanging from scalping to grading and vice-versa, machinery at VNR have screens that can be interchanged with the Pre-cleaners.
Gravity separator: Maintains uniformity of batch by separating light seed and heavy seed.
De-stoner: It enables easy and fast separation of stone, mud balls and uncoated seed. It works with negative pressure.
Super Cyclo Fan: Facilitates removal of dust from intake hopper and gravity separator. Also removes husk, chaffy and other similar material during pre-cleaner and fine cleaner stages. This helps in faster removal of dust, emits dust free air and keeps processing floor environment friendly.
Treator: Facilitates to mix chemicals in proportionate ratio with pre-defined quantity of seed. Helps to achieve uniform chemical coating of seed and avoids under or over treatment of chemicals.
Online Dryer: This process helps in removal of surface moisture after seed treatment and allows direct packing of seed. In this process, seed travels on a conveyor belt and hot air at 38 – 40 degree celcius in blown over it, followed by blowing of ambient temperature air to bring seed to normal temperature.
Z elevator and Feeder vibrator: To reduce mechanical damage and injury to seed, VNR has implemented Z elevator and feeder vibrator. Installed Z elevators have buckets based “gentle” seed handling. This process of transferring seed to next sequence of operation carries zero friction. Feeder vibrator avoids jamming of elevator thereby help in eliminating breakage of seed.
Packing: Seed is packed into various unit pack sizes from 5 grams to 10 kilograms depending upon type of crop and market requirement in primary pouch based packing thereafter, secondary packaging of window box and carton or polybag is done. VNR Processing line has integrated online facility to take an input of raw seed and give a final output of processed seed in packaged form, all in single flow. The advance packing machines are equipped with latest technology to ensure highest accuracy with weight precision through sophisticated multihead weigher, maintains excellent hygienic standards, reduces product wastage and facilitate tamper proof pouch sealing.
VNR Processing plants are equipped with technologically advance processing machines from world’s leading seed processing equipment manufacturer Cimbria Heid. VNR has two scalable—state of the art—vegetable and cereal crops processing facilities operational in India. First processing unit is based at Chhattisgarh – Durg District—having 2 Kirby PEB structure warehouses having an area of 50,000 & 34,000 square feet, it has 4 processing lines—first is having installed capacity of 10 tonnes per hour, second with capacity of 5 tonnes per hour for vegetables and foundation seed, third with capacity of 1 ton per hour and other smaller lines are for vegetable processing having capacity 50 Kgs. per hour. Second processing unit is based at Telangana, Bandamailaram having installed capacity of 5 tonnes per hour with kirby warehouse having 12000 sq feet capacity. Two types of seed drying machines are installed – For vegetables LPG base with capacity of 18 tonnes per batch and second is dehumidified drier with a capacity of 450 kgs. per batch. Pick & Pack and FFS packing machines are from Ishida, Yamato, Nichrome and Uflex, having capacity of 50 drops per minute. Crome color sorter is also installed at plant with sorting capacity of 300 – 400 kgs. per hour, this color sortex can identify & separate 16 types of color defects in vegetable seeds. It is equipped with full-color RGB cameras, NIR and LED lighting system.
There are 2 in house dehumidified cold storage with SCADA automation, maintaining temperature range of 12 – 14 degrees celsius and humidity range of 42 – 45%. First Cold storage is of 3 lakh cubic feet and having capacity of 1250 MT to store vegetables seed whereas second is of 22500 cubic feet having installed capacity of 65 MT. For pack seed storage, warehouse facility is equipped with scalable horizontal and vertical racking system. Warehouse in installed with centralized wireless LANs via Cisco Unified Wireless Network, which facilitates movement of barcoded packaged seed for shifting and dispatch in scan & validation mode. Further, both plants have redundant power backup from Cummins and secured leased line internet communication network. Facilities are well equipped with prescribed safety standards and dust free environment.
VNR is firm believer of process automation. Before taking up a workflow for automation, VNR Process Automation Team (V-PAT) ensures that first, process is made efficient, thereafter automation is applied. V-PAT always consider wider implications of adapted solution. Varied functions at plant have integrated applications, restructured resources, latest technologies implementation and uses ingeniously developed software applications – Seedtrac – with an objective to contain costs, automate complex business process, increase efficiency, minimize errors, save time and ensure critical processes are independent of person dependencies.
Processing plants at VNR are fully integrated and automated from input of raw seed to secondary packaging of condition seed. Processing machineries are infused with SCADA control system architecture that uses computers, networked data communications and graphical user interfaces for high-level process supervisory management. Use of sensors and software create smarter VNR processing facility. Automation has helped VNR achieve higher productivity, deliver consistent high quality and set up reliable control matrix.
At VNR Processing Plant, innovation means solving problems speedily and frugally. Targeting local resources, opportunities and being ingeniously, innovative is part of its DNA. Innovation fruits are the intersection of discipline and cultures, and VNR team with engaging, efficient and breakthroughs go beyond and apply principles of frugality, flexibility and instincts. VNR encourages bottom-up innovation approach, where team conjures to bring ideas to reality.
There are several innovative break throughs achieved over a period of time, some of them are:
- Integrated open source supply chain workflow automation software application – Seedtrac
- Barcode integration at secondary package level to ensure error free storage, retrieval and dispatch
- Proximity sensor based Pouch counting machine for error free packaging in window box
- Intelligent weight range check parameters to ensure that every master pack having correct weight and is not over or under weight
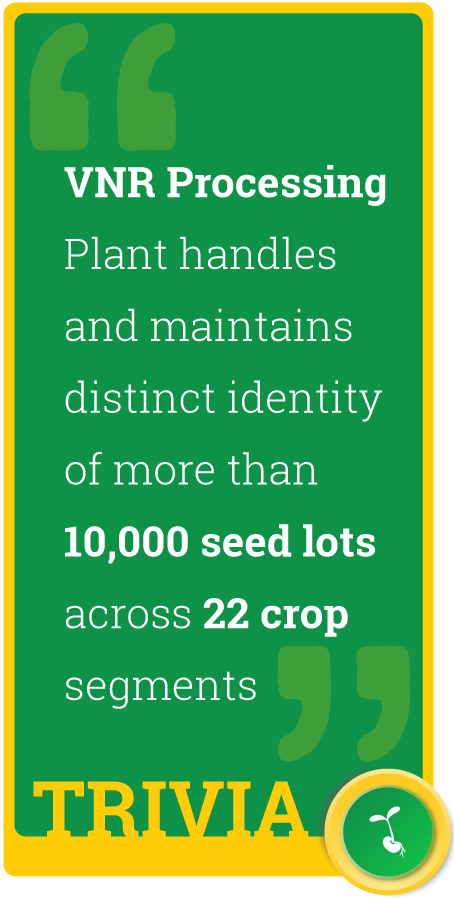